Tempered glass is obtained by cutting ordinary annealed glass to the required size first, and then heating to about 700 degrees close to the softening point, and then cooling quickly and evenly (usually 5-6MM glass is heated at a high temperature of 700 degrees for about 240 seconds and cooled down for about 150 seconds). 8-10MM GLASS IS HEATED AT 700 DEGREES FOR ABOUT 500 SECONDS AND COOLED DOWN FOR ABOUT 300 SECONDS. In short, depending on the thickness of the glass, the time to choose heating and cooling is also different). After tempering, uniform compressive stress is formed on the surface of the glass, and tensile stress is formed inside, so that the bending and impact strength of the glass can be improved, and its strength is about four times that of ordinary annealed glass. The tempered glass that has been tempered can no longer be cut, ground or damaged, otherwise it will be "shattered" due to the destruction of the uniform compressive stress balance.
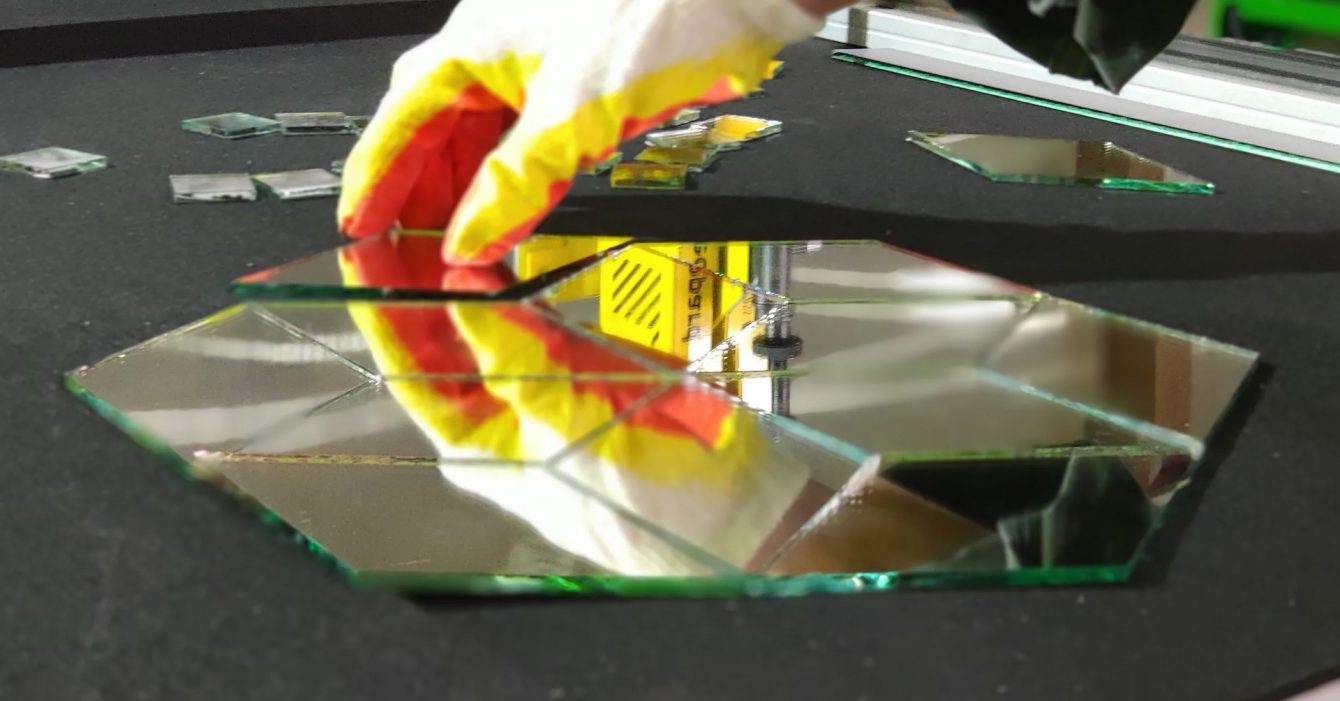